Automated Solution Keeps The Stockroom on Track
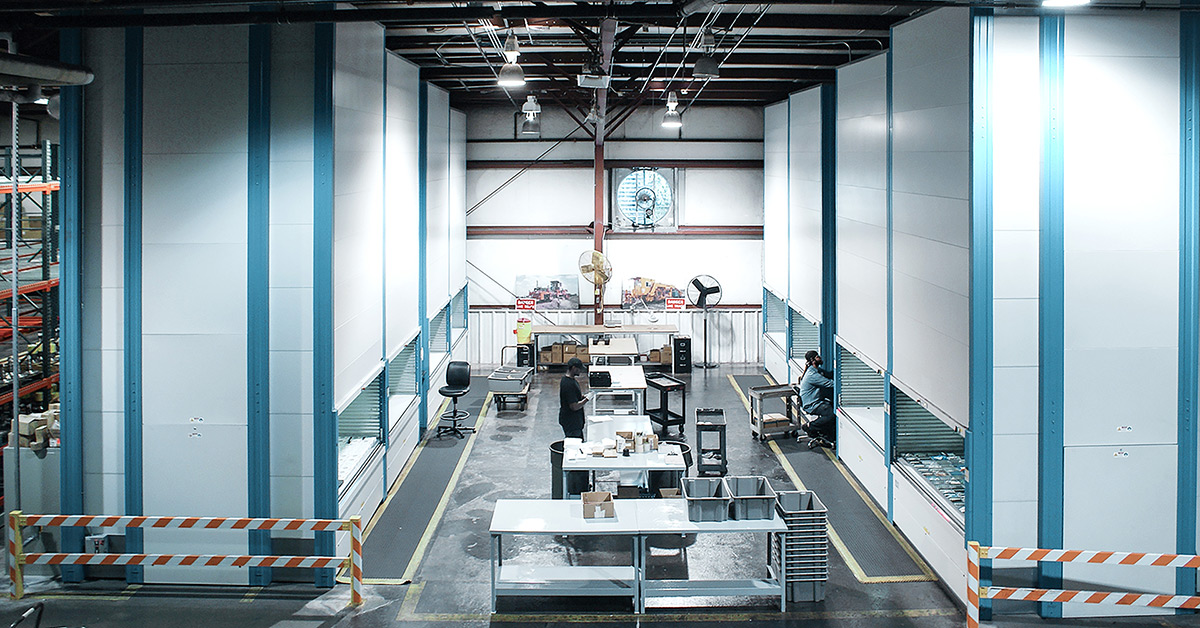
Plasser American, provides innovative cost-effective track maintenance solutions for the North American rail industry through safe and high-quality performance products and services. Supporting freight railroads and high speed intercity and commuter systems with machines designed to maintain, straighten, and strengthen existing railroads and transit systems, Plasser helps keep America running at top speed.
Their facility in Chesapeake, VA focuses on manufacturing of new machinery, as well as overhauling and upgrading services to extend the useful working life of machines, providing customers the benefit of the latest technologies and developments without the new price tag. The 35,000 square foot stockroom inventories over $16 million in spare parts with the support of 8 Vertical Lift Module (VLM) Kardex Shuttles with Kardex Power Pick System inventory management software.
The previous stockroom was split into two sections with the front section storing smaller parts and the back section storing larger parts. Using a list of printed labels, a worker would travel through the mezzanine bin shelving to each part location collecting the parts required.
With steady market growth and production operations at capacity, Plasser needed to expand production capacity to grow sales. They sought to consolidate the stockroom to make space for production.
The Solution
The stockroom replaced a sizable two-story mezzanine bin system with 8 Kardex Shuttles integrated with pick to light technology and Kardex Power Pick System. The original two-story mezzanine bin system had 19,000 square feet of shelving and occupied 4,875 square feet of floor space. With each VLM measuring just over nine feet wide and ten feet deep, the new stockroom with eight Kardex Shuttles and a pick area now occupies only 1,440 square feet of floor space, a 70% floor space savings.
With order volume and SKU count remaining the same, Plasser is picking with 20% less labor. “Since the parts are delivered to the operator for picking, our pick time per part has decreased, allowing us to pick the same number of orders with less labor” says Boone. The manual stockroom required ten people while the new automated stockroom requires only eight people.
Accuracy, Traceability & Counting
With 18,000 SKUs in inventory finding the right part can be challenging, but not at Plasser. The pick accuracy level has increased from 98% to 99.7%. “We attribute our increase in pick accuracy to the pick to light technology and our labeling process at receiving,” says Boone. As parts are received into the stockroom and put away, they are labeled with a barcode that identifies the part number and receipt number. This allows bar code scanning upon retrieval for near perfect accuracy.
Yearend inventory count was a tedious task in the mezzanine bin system. Now using the Kardex Power Pick System, parts are presented to the operator for cycle counting. The stockroom reported a $500 Kardex Shuttle inventory variance at the end of last year; only 0.01% in misplaced inventory.
![]() |
8 Kardex Shuttles |
![]() |
Kardex Power Pick System |
![]() |
Pick to light technology |