Kit & Component Management for Global Flight Simulator Manufacturer
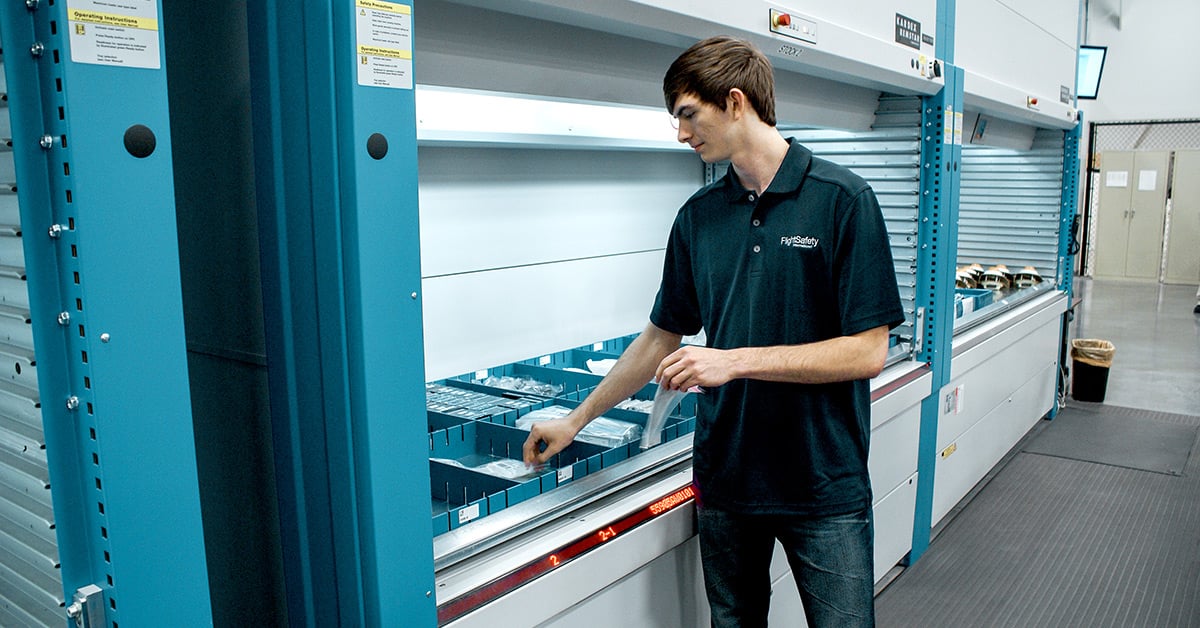
FlightSafety International is the world’s leading manufacturer of full flight simulators, visual systems and displays. With more than 40 Learning Centers worldwide, 1,800 instructors, 3,000 courses on 135 aircraft types, FlightSafety International provides over a million hours of training each year on a wide variety of aircraft types.
With demand on the rise, the stockroom needed more efficiency and control. “Component parts and kits were stored in cardboard boxes on shelving, making order fulfillment a time consuming, labor intensive process with inventory susceptible to shrinkage,” says Mike Halsey, Director of Manufacturing and Material Management. The stockroom was struggling to support the cutting-edge manufacturing line with their manual processes.
In coordination with a new facility the stockroom implemented four, 36 foot tall Vertical Lift Module (VLMs) Kardex Shuttles to manage components and kit inventory. The new automated picking and kitting process has reduced stockroom labor requirements by 86%, increased accuracy to 99.9% and reduced floor space by 85%.
The Solution
When FlightSafety moved into a new building, the stockroom was upgraded. Implementing four Kardex Shuttles reduced the footprint of the component and kitting areas in the new facility from roughly 6,454 square feet to 960 square feet, an 85% floor space savings.
Now, only one person is required in the components area and one person in the kitting area, compared to seven previously. With labor reduced by 86%, other workers have been reassigned to different areas of the warehouse to increase efficiencies. Additionally, there is limited to no opportunity for error. Integrated with pick-to-light technology, the operator is directed throughout the picking processing. “Accuracy is at 99.9% - up from the mid 90%’s,” says Halsey.
Kitting Zone
Upon arrival at kitting, the operator bar code scans each tote, placed at one of the 10 batch light positions, and the VLMs present a tray and uses the put-to-light to direct the operator to the exact location on the tray to store the kit. The kit can remain in the VLM buffer storage for up to 60- 90 days. The production floor sends a request to kitting to pull the appropriate kit number and the operator retrieves the kit requested from the Kardex Shuttle and delivers it to manufacturing.
![]() |
4 Kardex Shuttles | |
![]() |
|
|
![]() |
10 position batch station |