Simple Automated Samples Storage
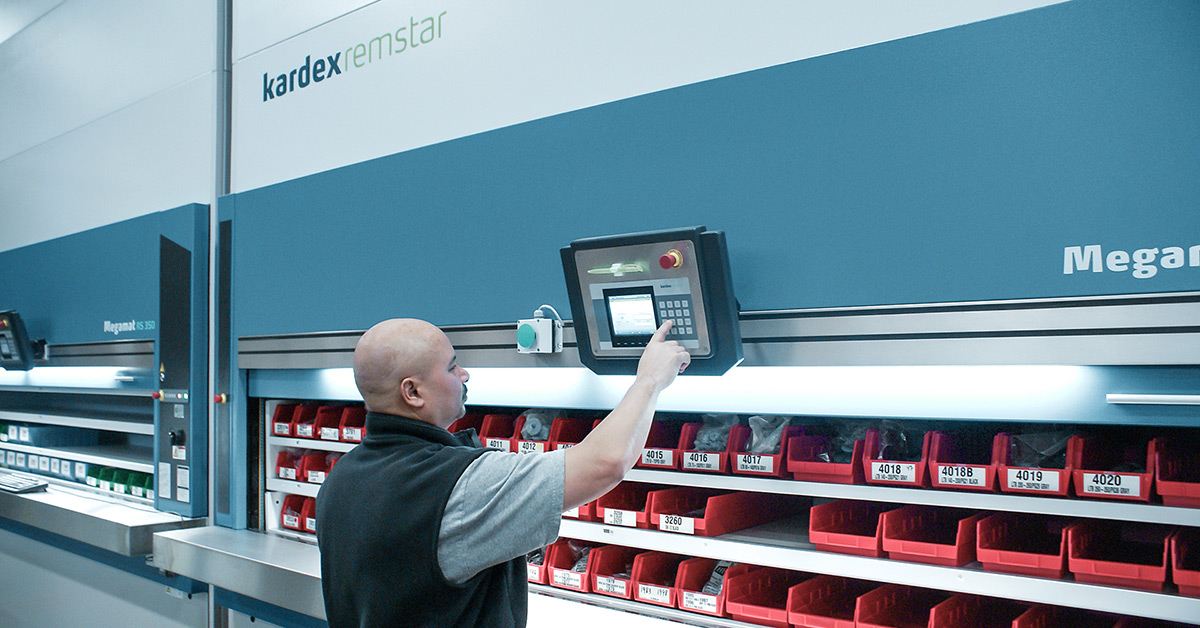
Heyco Products designs and manufactures molded wire protection products and stamped electrical components to meet demanding customer application requirements. Their prototyping technology along with high-volume manufacturing capabilities turns challenging “just-in-time” manufacturing deadlines into production realities. Heyco’s manufacturing facility in Toms River, NJ uses 2 Vertical Carousel Module Kardex Megamats to inventory over 18,000 sample SKUs.
With storage capacity at its limit; stocking, managing, picking and shipping sample orders was becoming a cumbersome and time-consuming process. Heyco previously uses 20-year-old carousels to manage the samples and frequent downtime was making it more and more time consuming to fill sample orders. “Sample orders are sometimes the first interaction customers have with Heyco, so it’s important that the right sample is delivered quickly to the customer,” said Colleen Faulknor, VP of Administration at Heyco.
The Solution
Heyco installed 2 new Kardex Megamats in the samples area. The Kardex Megamats are configured with carriers and totes to maximize capacity. “With the Kardex Megamats we can fill the same number of orders quicker and we’ve increased inventory capacity,” says Faulknor.
The previous carousels were 20 feet tall and provided 1,792 storage locations. The Kardex Megamats are 24 feet tall and provide 4,788 storage locations. Heyco increased sample storage capacity by 167% in the same footprint. “With that additional capacity we’ve gained, we will be able to sustain years of additional growth in our sample program,” says Faulknor.
With the push of a button the carousel rotates around to deliver the requested part to the samples clerk with limited wait time. “With regularly scheduled maintenance we’ve had zero unplanned downtime,” says Faulknor.
![]() |
2 Kardex Megamats |
![]() |
Logicontrol |