Electronics Manufacturer Integrates Ergonomic Automation
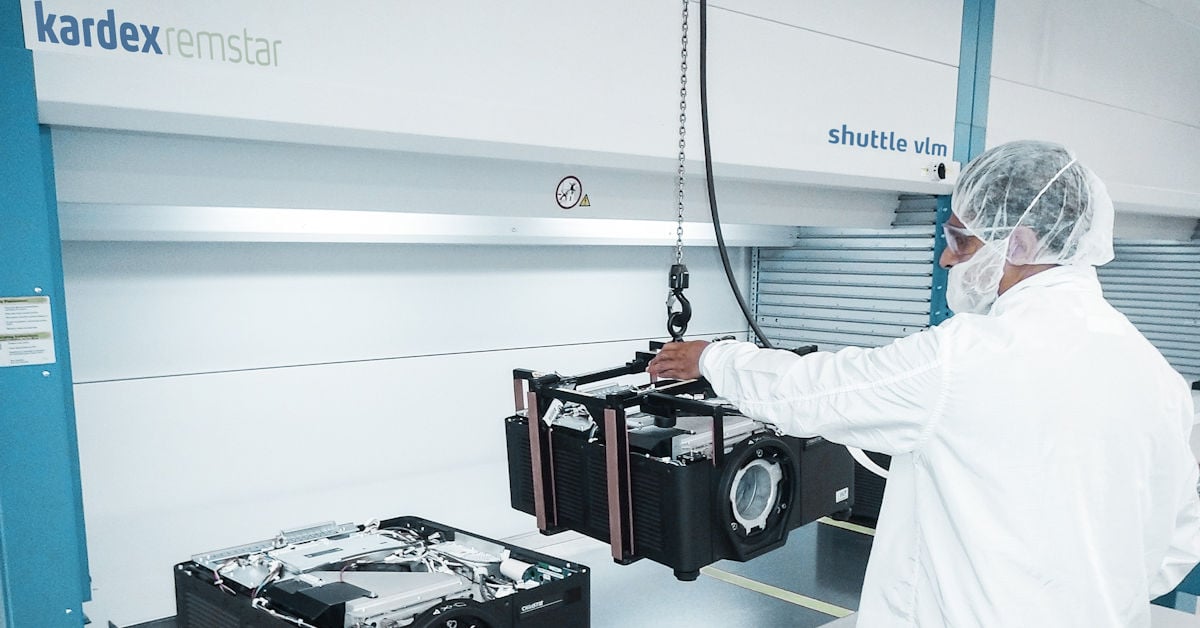
With over nine decades of experience Christie has a reputation of delivering superior visual display solutions and providing unprecedented levels of service and support. The certified ISO 9001:2000 and 14001 manufacturing center in Kitchener, Ontario houses top of the line technology including two Vertical Lift Module Kardex Shuttles each equipped with automatic tray extraction and crane handling.
With orders increasing, Christie needed to double the number of sub-assembled projectors they kept on hand. Previously, Christie maintained an inventory of 100 sub-assembled projectors, each stored on a cart. “To double inventory, we would have had to double the cart area, buy more carts and hire more people,” said Philip Hibberd, Sr. Manufacturing Engineer.
While increasing capacity and improving worker ergonomics were the main project focus, Christie also sought to give their customers the best of both worlds: custom built projectors with 24-hour order turnaround time.
The Solution
Christie installed 2 Kardex Shuttles each equipped with automatic tray extraction and crane handling. Each Kardex Shuttle stores 100 sub-assembled projectors, doubling capacity overnight. Both have expansion capacity, allowing inventory to increase based on sales.
Including the aisle, each Kardex Shuttle occupies 180 square feet, compared to the 600 square feet occupied previously - a 70% floor space savings. “The recovered space has been used to expand the sub-assembly process from 6 assembly stations to 9,” said Hibberd.
Each projector weighs around 52 pounds. “The projectors are heavy and lifting them puts the employee at risk of injury and the projector at risk of damage,” says Hibberd. Each Kardex Shuttle has automatic tray extraction, so all sub-assembled projectors are accessed with an ergonomic hoist; no lifting, pushing or pulling is required.
![]() |
2 Kardex Shuttles |
![]() |
Automatic tray extraction |
![]() |
Integrated crane handling |
![]() |
Kardex Power Pick System |